Home » Pallet Racking Layouts
Pallet Racking Layouts
When designing your warehouse pallet racking layouts there are four main components to consider:
1. The space occupied by the goods and the equipment on which they may be stored, with the necessary clearances.
2. The aisles between the goods, for direct access to the goods.
3. The gangways at the right angles to the aisles.
4. Any other areas, devoted to such things as marshalling of goods, loading and unloading of lorries, fire escape routes, clearances around heating systems etc.
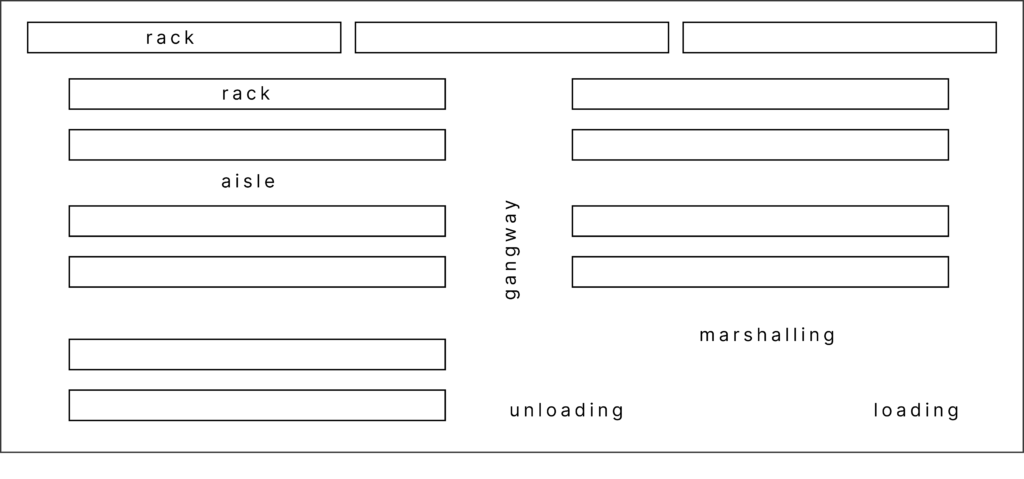
Normally, the goods are stored within the perimeter of the pallet. If not, the comments about pallets (below) will apply to the area occupied by the goods.
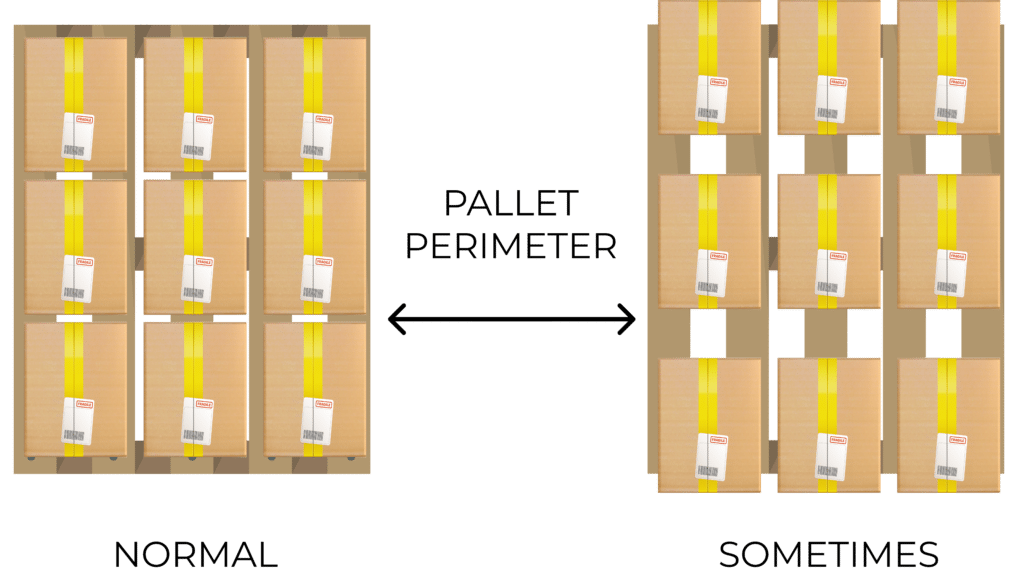
Aisle Widths
The width of the aisle is the clearance between the pallet, goods or racking, whichever clearance is the smallest:
The width of the aisle is determined by the type of forklift truck that will be used in the warehouse. The manufacturer usually gives this assuming a pallet size of 1200mm x 1000mm, though this may vary.
When calculating aisle widths you should always check the pallet size if it is larger then a bigger aisle will be required.
ALWAYS INCREASE THE MANUFACTURER’S RECOMMENDED AISLE BY AT LEAST 200MM.
Why?
Warehouse pallet racking layouts invariably involve a compromise between the use of the available space and the speed of the materials handling. Working to the manufacturer’s minimum aisles is like parking in a very tight parking space. It can be done, but it takes time and it can cause considerable wear on the vehicle and driver. It is reasonable to expect between 20 and 30 pallet movements in an hour. The throughput will be halved with restrictive aisles.
When calculating minimum aisle widths, fork truck manufacturers assume that pallets will be located as far back as possible on the fork and that pallets have been placed on racks accurately.
Assess Pallet Racking Layouts
The quick method to calculate the number of runs of pallet locations that can be positioned within your warehouse is explained below. The example shows a module consisting of one aisle + two pallets + the clearance between the back of the pallet can be used.
Gangways
Gangways are used to gain access to aisles.
The absolute minimum width of one gangway should be 1800mm. This permits only one forklift truck to use it at a time. Although this is more than sufficient for one truck to drive down, the space is needed for turning in and out of aisles.
If more than one fork lift is being used then the gangway should be 3000mm.
Gangways are basically dead space and they should be kept to a minimum. Consequently, the best utilisation of space is usually achieved when the racking runs in the same direction as the longest dimension of the space. This rule holds true in 90% of cases.
The number of gangways is frequently determined by the requirements of the Fire Officer and Fire Escape routes.
This example would be rejected because there are aisles with access from only one end, causing dead ends or blind alleys.
Thus there should normally be gangways at the end of the aisles.
It is possible, of course, to convert a gangway into an aisle like the image below.
The number of gangways required – (which then determine the length of the racks) is established by factors such as the amount of access required, the number of forklifts in use and the positioning of the marshalling area.
However, the racks should not exceed 30 metres in length. Longer than this can cause the effectiveness of forklift truck drivers to decrease and problems such as difficulty locating pallet positions and greater distance penalties for choosing the wrong aisles could arise.
Beams and Uprights
The beam length is calculated by the number of pallets per beam x left – to – right dimension of pallet, plus at least 75mm clearance between each pallet, and 75mm clearance between pallet and frame.
This example shows 2 x UK specification pallets at 1200m x 1000mm sitting side by side.
2 x 1200 = 2400 + 3 x 75mm
= 2400 + 225 = 2625mm
75mm minimum clearance as this allows for 100mm clearance when your beam level exceeds 6000mm.
Our standard is 2700mm.
When calculating a run length it is important to also allow for the width of the uprights.
If you have any other queries regarding Pallet Racking Layouts, please do not hesitate to contact us. Or take a look at our technical hub for more topics.
RediRack are full members of SEMA (Storage Equipment Manufacturers Association), with our installation and inspection teams fully SARI (SEMA Approved Rack Inspector), and SEIRS (Storage Equipment Installers Registration Scheme) registered.